Diesel Generator for Factory Acceptance Testing Ensuring Reliability and Performance in Industrial Settings
Introduction
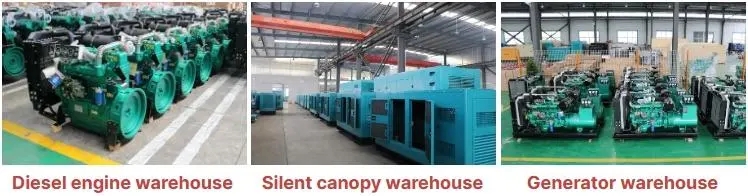
Diesel generators play a critical role in providing backup power to industrial facilities in the event of grid power outages. These generators are essential for ensuring uninterrupted operation of critical equipment and processes in factories, manufacturing plants, and other industrial settings. To ensure the reliability and performance of diesel generators, it is essential to conduct thorough factory acceptance testing before the equipment is deployed in the field.
In this article, we will explore the importance of factory acceptance testing for diesel generators, the key components of such testing, and best practices for conducting these tests to guarantee the optimal performance of the equipment in industrial environments.
Importance of Factory Acceptance Testing
Factory acceptance testing (FAT) is a crucial step in the commissioning process of diesel generators for industrial applications. 300kw diesel generator for oil and gas facilities of FAT is to verify that the equipment meets the specified design and performance requirements before it is delivered to the customer's site. By conducting FAT, manufacturers can identify and rectify any issues or defects in the equipment in a controlled environment, thus minimizing the risk of failures or malfunctions in the field.
For diesel generators used in industrial settings, the consequences of equipment failure can be severe, leading to costly downtime, production losses, and potential safety hazards. Therefore, ensuring the reliability and performance of diesel generators through rigorous FAT is essential for maintaining operational continuity and minimizing risks to personnel and assets.
Key Components of Factory Acceptance Testing
Factory acceptance testing for diesel generators typically involves a series of tests and inspections to evaluate various aspects of the equipment's performance, functionality, and compliance with specifications. The key components of FAT for diesel generators include:
1. Functional Testing: Functional testing involves verifying that the diesel generator can start, run, and operate as intended under different load conditions. This includes testing the generator's ability to supply power to critical loads, transfer power seamlessly in case of grid failures, and shut down safely when required.
2. Performance Testing: Performance testing is conducted to assess the generator's output capacity, voltage regulation, frequency stability, and fuel efficiency under varying load conditions. This helps ensure that the generator can meet the power demands of the industrial facility and maintain stable operation throughout its intended service life.
3. Safety Testing: Safety testing is essential to evaluate the diesel generator's compliance with industry standards and regulatory requirements for electrical and mechanical safety. This includes checking for proper grounding, insulation resistance, overcurrent protection, and emergency shutdown mechanisms to prevent accidents and hazards.
4. Environmental Testing: Environmental testing assesses the generator's performance under different environmental conditions, such as temperature extremes, humidity levels, and vibration resistance. This is particularly important for industrial settings where generators may be exposed to harsh operating environments.
5. Control System Testing: Control system testing involves evaluating the functionality of the generator's monitoring and control systems, including the user interface, alarms, automatic start/stop sequences, and remote monitoring capabilities. This ensures that operators can effectively control and monitor the generator's operation to prevent failures and optimize performance.
Best Practices for Conducting Factory Acceptance Testing
To ensure the success of factory acceptance testing for diesel generators, manufacturers and customers should follow best practices to effectively evaluate the equipment and address any issues that may arise. Some key best practices for conducting FAT include:
1. Define Clear Acceptance Criteria: Before conducting FAT, it is essential to establish clear acceptance criteria based on the equipment specifications, performance requirements, and industry standards. This ensures that both the manufacturer and the customer have a common understanding of the expected outcomes of the testing process.
2. Involve Stakeholders: FAT should involve key stakeholders from both the manufacturer and the customer, including engineers, project managers, and operators. This collaborative approach ensures that all parties are aligned on the testing procedures, objectives, and outcomes, and facilitates effective communication throughout the testing process.
3. Create a Comprehensive Test Plan: A detailed test plan should be developed outlining the specific tests to be conducted, the test procedures, acceptance criteria, and responsibilities of each party involved. The test plan should cover all aspects of the generator's performance, functionality, safety, and compliance with standards.
4. Conduct Systematic Testing: During FAT, testing should be conducted systematically, following the test plan and procedures outlined. Each test should be documented, and the results recorded for analysis and verification. Any deviations or issues encountered during testing should be documented and addressed promptly.
5. Verify Compliance with Standards: Diesel generators for industrial applications are subject to various industry standards and regulations, such as the National Fire Protection Association (NFPA) standards, Occupational Safety and Health Administration (OSHA) regulations, and local electrical codes. FAT should verify that the generator complies with these standards to ensure safe and reliable operation.
6. Address Non-Conformities: In case of any non-conformities or failures identified during FAT, manufacturers should take corrective actions to rectify the issues and retest the equipment to ensure compliance with specifications. It is essential to document all non-conformities, corrective actions taken, and verification of the remedial measures.
7. Provide Training and Documentation: As part of FAT, manufacturers should provide training to operators and maintenance personnel on the proper operation, maintenance, and troubleshooting of the diesel generator. In addition, comprehensive documentation, including operation manuals, maintenance schedules, and spare parts lists, should be provided to support the safe and efficient use of the equipment.
Conclusion
Factory acceptance testing is a critical step in ensuring the reliability and performance of diesel generators for industrial applications. By conducting thorough testing of the equipment before deployment, manufacturers and customers can identify and address any issues or defects that may impact the generator's operation in the field. Following best practices for FAT, such as defining clear acceptance criteria, involving stakeholders, creating a comprehensive test plan, and verifying compliance with standards, is essential for achieving successful testing outcomes.
In conclusion, factory acceptance testing plays a vital role in guaranteeing the optimal performance of diesel generators in industrial settings, enabling businesses to maintain operational continuity, mitigate risks, and ensure the safety of personnel and assets. By following established testing procedures and best practices, manufacturers and customers can enhance the reliability, efficiency, and longevity of diesel generators, contributing to the overall productivity and resilience of industrial facilities.